Inside Workwear Industry Procedure
The workwear industry manufactures various product assemblies and all kinds of necessary accessories used in all industries and uses all kinds of procedures to check the standards, design, various sizes and quality for the safety of all kinds of products by using the high-tech calculations so that they fully meet the requirements of customers.
The Global Workwear Industry Procedures
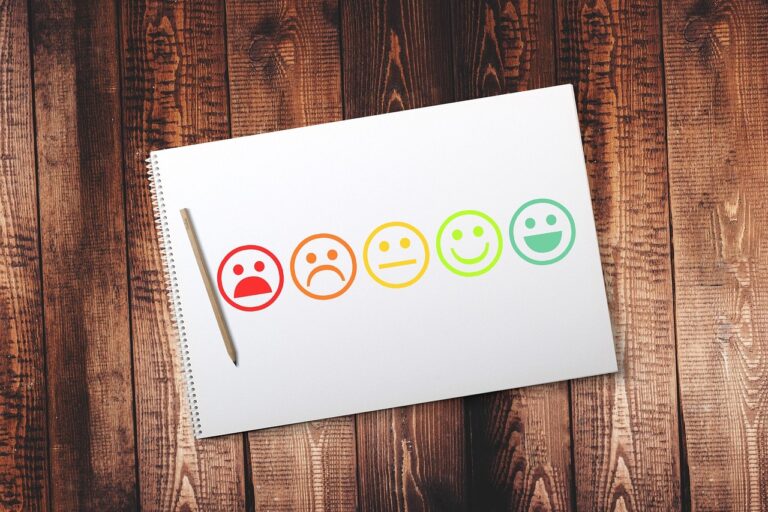
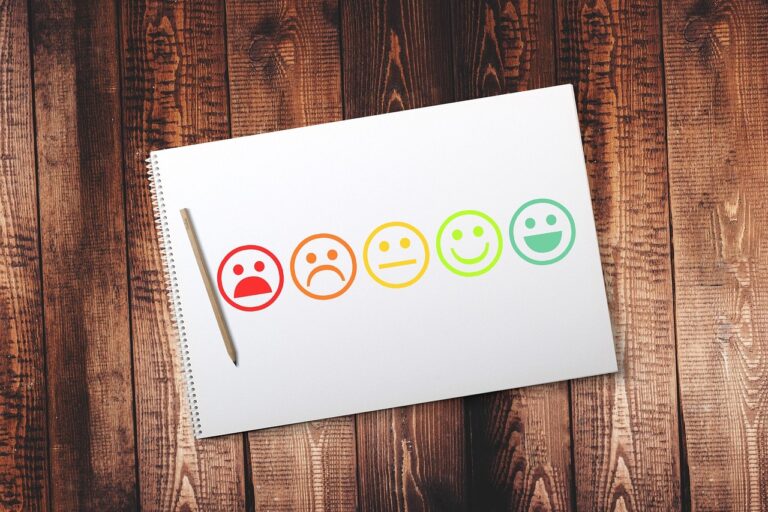
Global Feedbacks and Implementations Standards
Workwear feedback and implementation involve collecting input from workers who wear the gear daily to improve design, comfort, and functionality. Feedback may cover issues like fit, durability, breathability, or ease of movement.
The Workwear Industry Procedure
From Concept to Global Shipment
The workwear industry is dedicated to producing durable, comfortable, and protective clothing for workers in various sectors. From construction to healthcare, each piece of workwear is designed to meet the unique demands of the job. Here’s a detailed breakdown of the process that goes into creating high-quality workwear, ensuring that every step—from initial proposal to global delivery—meets the highest standards.
1. Proposal and Understanding Customer Requirements
The journey begins with understanding the customer’s specific needs. The first step in the process is gathering detailed requirements from the client. This involves understanding the nature of the work environment, safety regulations, preferred materials, and any customizations such as company logos or branding. Clients may request specific features like flame resistance, water resistance, or high-visibility fabrics based on the industry they serve. At this stage, our team works closely with the client to define the scope of the project, the necessary materials, and any special requirements for comfort or performance.
Once the customer’s needs are understood, a proposal is drafted that outlines the design, materials, production timeline, and cost estimates. This proposal serves as the foundation for the workwear design, ensuring that all parties are aligned on expectations.
2. Designing and Cutting According to Sizes
After the proposal is approved, the design process begins. Designers work closely with clients to create workwear that is not only functional but also comfortable and stylish. They take into account the specifics of the work environment, considering factors such as ease of movement, durability, and the overall look. Designers often use CAD (Computer-Aided Design) software to create detailed blueprints for each item of workwear, from jackets to pants and protective gear.
Once the designs are finalized, it’s time to prepare the cutting patterns. Using the customer’s specified sizes and measurements, patterns are created for each garment. Whether it’s a small size or an extra-large size, precise measurements are crucial to ensure a perfect fit and maximum comfort for the wearer.
Cutting machines or skilled hands then cut the fabric into these patterns, ensuring that each piece is uniform and accurate, which is essential for maintaining quality and consistency throughout the entire batch.
3. Raw Materials Collection and Suppliers
The quality of workwear is only as good as the raw materials used. At this stage, the necessary materials are sourced from trusted suppliers. Workwear fabrics such as cotton blends, polyester, ripstop, and high-performance materials like Gore-Tex, Kevlar, and flame-resistant fabrics are chosen based on the customer’s requirements.
Quality is key, and suppliers are carefully selected for their ability to deliver materials that meet stringent safety and performance standards. For instance, flame-resistant fabric must pass specific tests to ensure it offers adequate protection in high-risk environments. Similarly, waterproof materials are selected for their ability to resist water while maintaining breathability, which is important for worker comfort.
Raw materials like zippers, buttons, thread, and reflective tape are also sourced at this stage. Suppliers for these components must adhere to strict quality standards to ensure durability and functionality.
4. Stitching – Step by Step
Once all materials are collected, the stitching process begins. Skilled workers or advanced stitching machines come into play to assemble the pieces of the workwear. Here’s a step-by-step breakdown of the stitching process:
- Preparation: The fabric pieces are laid out in the correct order and aligned to ensure precision.
- Sewing: Using heavy-duty sewing machines, workers carefully stitch together the main sections of the garment. For example, the body of the jacket is sewn to the sleeves, and pockets are added where needed.
- Reinforcement: Areas that endure more wear and tear, like the elbows, knees, and cuffs, are reinforced with double stitching or additional layers of fabric for extra durability.
- Finishing Touches: Reflective strips, logos, and other custom features are sewn onto the garments. The final touch is checking for any loose threads or stitching defects before moving the garment to the next step.
The stitching process is a blend of craftsmanship and technology. Quality control checks are carried out throughout to ensure that every piece meets the specifications set out in the proposal.
5. Global Testing
Standard | Description | Typical Regions |
---|---|---|
ISO 6330, ISO 15797 | Domestic/industrial wash testing | Global labs worldwide |
ISO 20471, ANSI/ISEA 107 | Hi‑visibility garment & tape testing | EU, USA, Canada, AU/NZ, Asia |
ASTM D6413, NFPA 2112 | Flame resistance for fabrics/trims | North America, globally via UL/SATRA |
ISO 11092, ASTM F1868 | Thermal comfort testing | International labs |
ISO 13034, EN 6530 | Chemical splash protection | EU, USA, Canada, Japan |
ISO 12127, EN 11612 | Contact/heat resistance | Europe, global agencies |
ISO 20344 series | Footwear safety + reflective integration | EU, global via SATRA/TÜV |
5. Packaging
After the workwear is stitched and passes quality inspection, it’s ready for packaging. Proper packaging is essential to preserve the quality of the garments during transportation and to make sure they arrive in pristine condition. Each garment is carefully folded or rolled, depending on the design, and packed in protective plastic or eco-friendly packaging. For bulk orders, the items are grouped into boxes or cartons, with clear labeling that includes the type, size, and quantity of each garment.
To ensure the garments reach the customer in perfect condition, the packaging process includes measures to prevent any damage during transit, such as padding or air-tight seals to protect from moisture or dust.
6. Means of Shipment for Global Delivery
Once packaged, the workwear is ready to be shipped worldwide. The shipment process is carefully coordinated to meet the needs of customers, whether they’re located across the country or on the other side of the world. For international shipments, trusted logistics partners and couriers are selected based on their ability to provide fast, reliable, and cost-effective service.
Air freight is often used for fast delivery of urgent orders, while sea freight is more economical for larger, bulk shipments. For customers in closer regions, land transport is used to ensure prompt delivery. Each shipment is tracked to provide customers with up-to-date information on the location of their order, giving them peace of mind from the moment the products leave the warehouse until they arrive at their destination.
For customs clearance, all necessary documentation is provided to ensure smooth international transactions, adhering to the laws and regulations of the destination country. With reliable shipping options and efficient delivery times, workwear reaches clients around the globe, ensuring that employees are equipped with high-quality clothing for the toughest jobs.
Conclusion
From the moment a customer expresses interest to the final delivery of their workwear, the entire process is driven by quality, efficiency, and customer satisfaction. Every step, from proposal and design to stitching, packaging, and shipment, is crucial in ensuring that workers receive clothing that meets their specific needs. In today’s competitive market, the workwear industry is constantly evolving to integrate new technologies, better materials, and faster shipping methods, making it easier than ever for businesses to get the protection and comfort their workers need, wherever they are in the world.
Inside Workwear Inventions
Due to the high requirements for Weather Protection and Safety, we use the latest Technologies, Industry tests and ISO standards as well as the Certification of each individual item to create a solution that meets the customer’s requirements.