Inside workwear Procedure
Materials Collection
A comprehensive guide on materials collections used in workwear covering raw materials, fabrics, reflective tapes, design patterns, colors, and manufacturing steps.
Materials Collection
Explore the comprehensive process of designing and manufacturing workwear for various industries, including healthcare, firefighting, security, and construction. We have all important detailed information on raw materials in workwear, cotton vs. polyester workwear fabrics, global fabric sourcing and fabric weave patterns workwear, ripstop fabric colors, high‑visibility fabrics and also get more knowledge about reflective tape types, reflective tape color options, workwear reflective tapes manufacturing. Learn about workwear design patterns, reflective tape placement workwear, workwear color combinations and workwear manufacturing process, high‑visibility garment steps, raw material sourcing global inside workwear.
Article 1: “The Ultimate Guide to Raw Materials in Workwear”
Properties
- Raw Materials Overview
- Material Properties & Color Applications
- Manufacturing Steps Inside a Workwear Plant
- Global Sourcing Locations
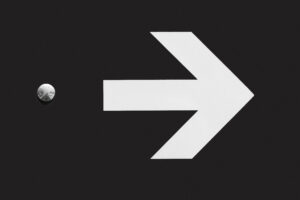
Raw Materials Overview
Cotton (USA, India, Brazil, Uzbekistan) – breathable, soft, natural.
Polyester (China, South Korea, Taiwan) – durable, moisture‑wicking.
Nylon (USA, Japan, South Korea) – abrasion‑resistant.
Wool (Australia, New Zealand) – thermal, flame‑resistant.
Aramid® (Kevlar®, Nomex®) (USA, Europe, Japan) – high‑strength, cut‑ and heat‑resistant.
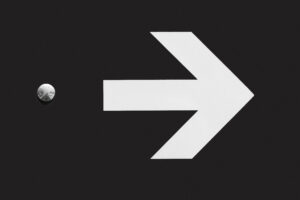
Material Properties & Color Applications
Cotton: dyes in bright yellow & navy—easy bleaching
Polyester/nylon: vivid hi‑vis orange/green, retains brightness
Aramid: limited palette—natural, charcoal, black
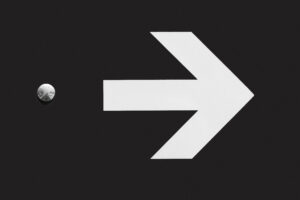
Manufacturing Steps Inside a Workwear Plant
Fiber reception – bale inspection, moisture testing
Blending & carding – uniform fiber mix
Spinning – ring/spinning frame
Weaving/knitting – shuttle/rapier looms
Scouring – deters oils/resins
Dyeing – jet/dyeing beck
Finishing – wrinkle/fluorocarbon treatments
Cut & sew – CAD cutting, edge‑sewing
Quality control – seam/pull‑test, colorfastness
Packaging & dispatch
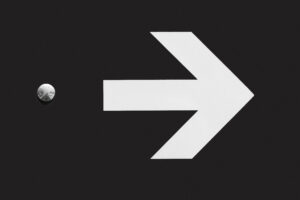
Global Sourcing Locations
Material
Major Source : Countries
Cotton : USA, India, China, Brazil
Polyester : China, Taiwan, S. Korea, Turkey
Nylon : USA, Japan, S. Korea
Wool : Australia, New Zealand, UK
Aramid : USA, EU, Japan
Article 2: “Fabrics & Weaves in High‑Performance Workwear”
Properties
- Fabric Types
- Design Patterns & Colors
- Fabric Production Flow Inside Mill
- Source Locations
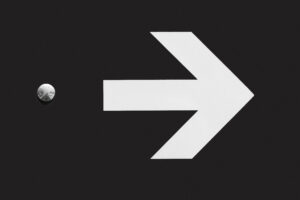
Fabric Types
Twill – diagonal lines, durable, seen in denim
Rip‑stop – added grid yarns for snag resistance
Canvas/duck – plain‑weave, heavy-duty
Knits (interlock, jersey) – flexible linings, high comfort
Non-wovens – flame‑retardant (FR) laminates like Gore‑Tex®, Sympatex®
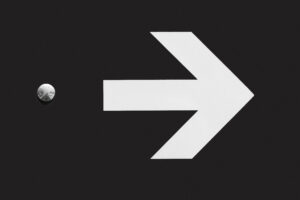
Design Patterns & Colors
Checkerboard rip‑stop in hi‑vis green
Twill with contrast stripes near knee/seams
Canvas patchwork in anthracite+orange
FR laminate linings in neutral grey
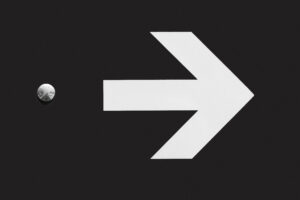
Fabric Production Flow Inside Mill
Fiber opening & blending
Yarn spinning
Weft insertion & weaving/knitting
Grey fabric inspection
Dye/print processes – jet dye, pigment print
Finishing – calendaring, DWR, heat-set
Final QC – tensile, tear, colorfastness
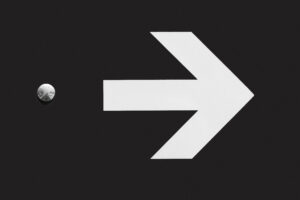
Source Locations
Rip‑stop: China, Taiwan, Vietnam
Canvas: Egypt, Turkey
Non‑wovens (FR): USA, Germany
Article 3: “Reflective Tapes in Workwear: Types, Applications & Colorways”
Properties
- Reflective Tape Types
- Color & Pattern Choices
- Manufacturing Workflow
- Global Production Hubs
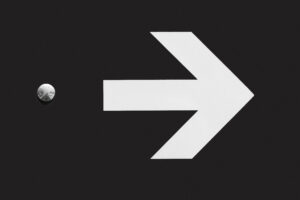
Reflective Tape Types
Glass-bead retro‑reflective – silver/fluorescent base
Micro-prismatic – stronger, longer durability
Magnetic/toggle‑patched – for modular uniforms
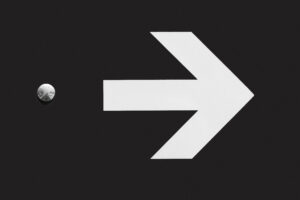
Color & Pattern Choices
Classic 2‑inch silver stripe on hi‑vis yellow/green
Chevron angled prismatic in dia‑stripes on navy
Dual-tone bands (orange + silver) for multi-risk sectors
Custom logos embedded in tape
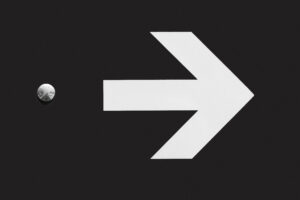
Manufacturing Workflow
Core film extrusion
Retro‑reflective layer application – beads/prisms
Adhesive lamination (heat or PSA)
Color pigmented coating
Slitting & quality check (adhesion, reflectivity)
Min. roll packaging
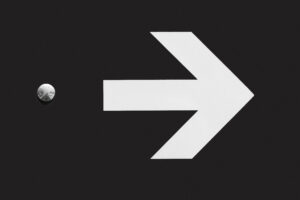
Global Production Hubs
Glass‑bead tape: USA, Germany, Japan
Prismatic tape: China, S. Korea, EU
PSA/backed tape: Taiwan
Article 4: “Design Styles & Color Schemes in Modern Workwear”
Properties
- Common Design Patterns
- Color Palettes
- Manufacturing Steps
- Design Origin Locations
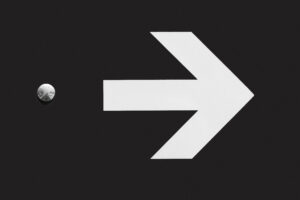
Common Design Patterns
Classic stripes on arms/chest
Chevron back design on jackets
Block‑color panels on legs/jackets
Integrated FR hooded sets with coordinated contrast
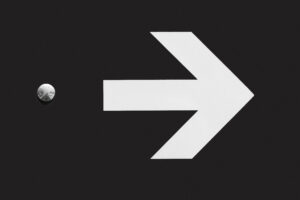
Color Palettes
Business utility: navy + hi‑vis accents
Industrial: charcoal + silver/amber
Forest/logging: camouflage panels with reflective chevrons
Construction: orange + lime + silver triple bands
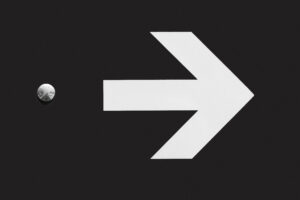
Manufacturing Steps
Pattern-making / CAD layout
Color‑block cutting
Tape placement heat‑press or stitch
Panel assembly – top‑stitch processes
Seam sealing / FR taping
Labeling & barcoding
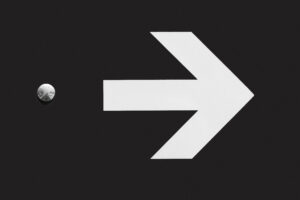
Design Origin Locations
Pattern drafting: Germany, Italy
Tape placement: Poland, Vietnam
Assembly plants: Bangladesh, Turkey, Mexico
Article 5: “From Fiber to Finished Garment: Workwear Manufacturing Workflow”
Properties
- Fiber to Yarn
- Fabric Stage
- Accessory Integration
- Garment Assembly
- Packaging & Global Supply
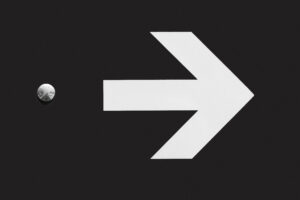
Fiber to Yarn
Cotton/Aramid/polyester converted in initial spinning mills (China, India, USA)
The production process begins with converting raw fibers such as cotton, aramid, or polyester into yarn. This initial spinning stage takes place in major textile-producing countries like China, India, and the USA, where advanced spinning mills ensure consistent quality and output.
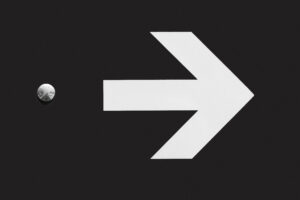
Fabric Stage
Weaving/Knitting – Turkey, Portugal, Malaysia
Dyeing & Finishing – Italy, South Korea (DWR, FR, soft touch)
Yarns are woven or knitted into fabric in countries like Turkey, Portugal, and Malaysia, known for their textile craftsmanship. The fabric then undergoes dyeing and finishing processes in Italy and South Korea, where specialized treatments such as durable water repellent (DWR), flame resistance (FR), and soft-touch finishes are applied.
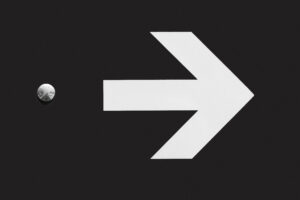
Accessory Integration
Reflective tape slots – adhesive or stitched
Zippers, buttons, rivets – sourced: YKK Japan, SBS China
Key garment components like reflective tape are integrated either through adhesive bonding or stitching. Additional accessories such as zippers, buttons, and rivets are sourced from reliable suppliers including YKK (Japan) and SBS (China) to ensure durability and performance.
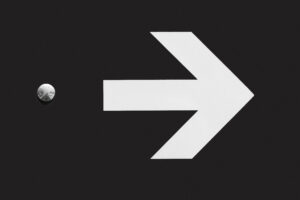
Garment Assembly
Cutting – CNC or manual
Binder/edge stitching – pre-assembled fabric
Reflective tape welding/stitching
FR seam sealing
Final inspection & packaging
Garment production involves precision cutting—done either manually or with CNC machines—followed by stitching and assembling of fabric panels. Reflective tapes are welded or stitched into place, flame-retardant seams are sealed, and each garment undergoes a thorough final inspection before packaging.
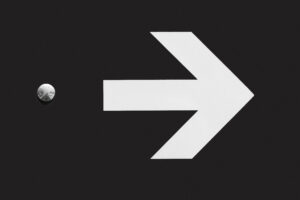
Packaging & Global Supply
Primary packaging in production country
Regional distribution hubs: Rotterdam (EU), Dubai (Middle East), Savannah GA (USA)
Finished garments are packaged in the country of production, then shipped to strategic regional distribution hubs. These include Rotterdam for the EU market, Dubai for the Middle East, and Savannah, Georgia for the USA, ensuring efficient global supply chain coverage.